Read the full Evidence Matters Newsletter HERE.
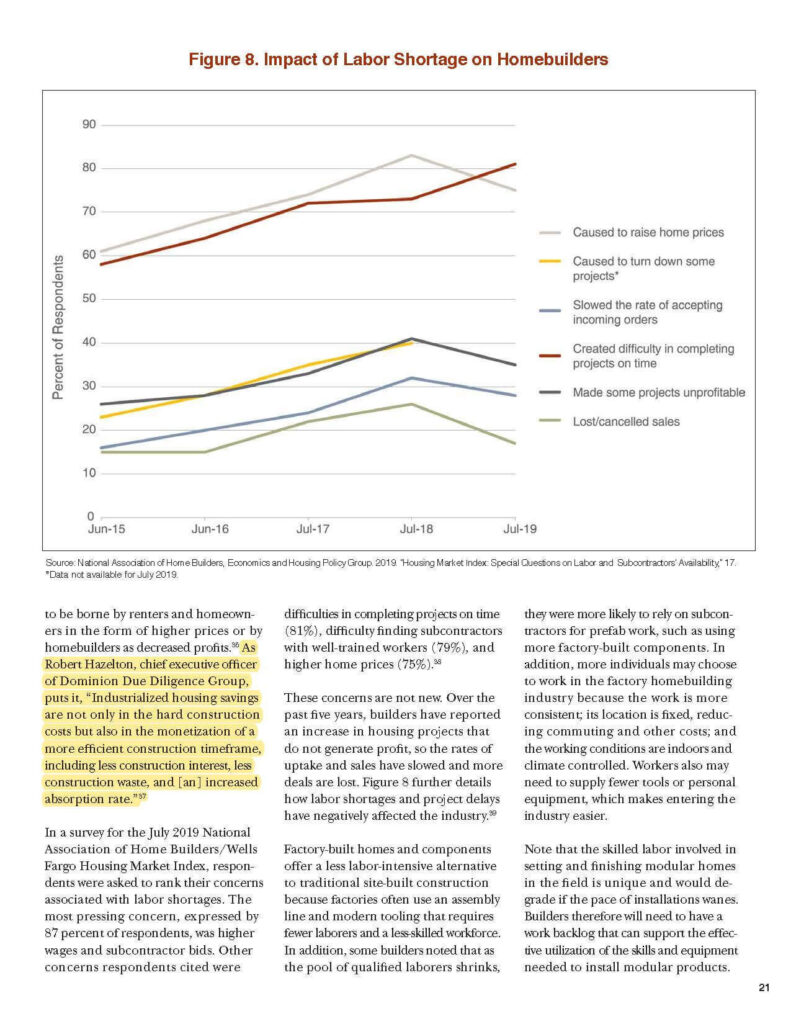
“…to be borne by renters and homeowners in the form of higher prices or by
homebuilders as decreased profits. (36) As Robert Hazelton, chief executive officer of Dominion Due Diligence Group, puts it, “Industrialized housing savings are not only in the hard construction costs but also in the monetization of a more efficient construction timeframe, including less construction interest, less construction waste, and [an] increased absorption rate.” (37)
In a survey for the July 2019 National Association of Home Builders/Wells Fargo Housing Market Index, respondents were asked to rank their concerns associated with labor shortages. The most pressing concern, expressed by 87 percent of respondents, was higher wages and subcontractor bids. Other concerns respondents cited were
difficulties in completing projects on time (81%), difficulty finding subcontractors with well-trained workers (79%), and higher home prices (75%). (38)
These concerns are not new. Over the past five years, builders have reported an increase in housing projects that do not generate profit, so the rates of uptake and sales have slowed and more deals are lost. Figure 8 further details how labor shortages and project delays have negatively affected the industry. (39)
Factory-built homes and components offer a less labor-intensive alternative to traditional site-built construction because factories often use an assembly line and modern tooling that requires fewer laborers and a less-skilled workforce. In addition, some builders noted that as the pool of qualified laborers shrinks,
they were more likely to rely on subcontractors for prefab work, such as using more factory-built components. In addition, more individuals may choose to work in the factory homebuilding industry because the work is more consistent; its location is fixed, reducing commuting and other costs; and the working conditions are indoors and climate controlled. Workers also may need to supply fewer tools or personal equipment, which makes entering the industry easier.
Note that the skilled labor involved in setting and finishing modular homes in the field is unique and would degrade if the pace of installations wanes. Builders therefore will need to have a work backlog that can support the effective utilization of the skills and equipment needed to install modular products.”